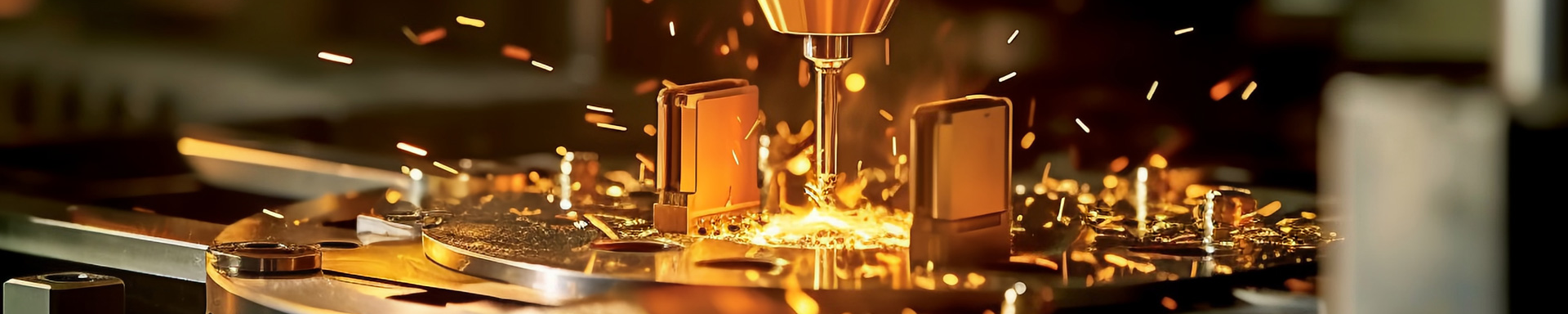
Poinçons de forme de précision
2024-11-28 16:54Sélection des matériaux et son impact
Le matériau choisi pour un insert de poinçon de forme de précision a un impact direct sur sa durée de vie, ses performances et la qualité de la pièce emboutie. Les matériaux courants comprennent les aciers à outils tels que l'acier rapide (HSS), les aciers à outils de métallurgie des poudres (PM) et le carbure. L'acier HSS offre un bon équilibre entre résistance, ténacité et rentabilité, ce qui le rend adapté à une large gamme d'applications. Cependant, sa résistance à l'usure peut être limitée par rapport à d'autres options. Les aciers à outils PM présentent une résistance et une résistance à l'usure améliorées en raison de leur microstructure contrôlée, ce qui se traduit par une durée de vie de l'outil plus longue et une précision dimensionnelle améliorée. Les inserts en carbure, bien que nettement plus chers, offrent une dureté et une résistance à l'usure exceptionnelles, idéales pour les séries de production à grand volume impliquant des matériaux extrêmement durs ou des géométries complexes.
Le processus de sélection prend également en compte des facteurs autres que le type de matériau. La nuance spécifique d'acier ou de carbure, les processus de traitement thermique et les revêtements de surface jouent tous un rôle important dans l'optimisation des performances de la plaquette et la prolongation de sa durée de vie. Par exemple, un revêtement spécialisé comme le nitrure de titane (TiN) peut améliorer considérablement la résistance à l'usure et réduire le frottement, ce qui conduit à une précision accrue et à des taux de production accrus. Le choix du matériau est donc une décision technique cruciale, équilibrant soigneusement le coût, la durabilité et les exigences spécifiques de l'opération d'emboutissage.
Considérations de conception et précision géométrique
La conception d'un insert de poinçonnage de précision est loin d'être arbitraire. Il doit refléter avec précision la forme souhaitée de la pièce emboutie finale tout en tenant compte de facteurs tels que l'épaisseur du matériau, les tolérances requises et le processus d'emboutissage global. Les logiciels de conception assistée par ordinateur (CAO) jouent un rôle crucial dans ce processus, permettant une modélisation et une simulation précises des performances de l'insert avant la fabrication réelle. Cela minimise le risque de défauts de conception et permet une optimisation efficace.
La précision géométrique est primordiale. De minuscules variations dans les dimensions de la plaquette peuvent entraîner des écarts importants dans la pièce emboutie, la rendant potentiellement inutilisable. Des techniques de fabrication avancées telles que l'usinage par électroérosion (EDM) et la découpe au laser garantissent les plus hauts niveaux de précision, permettant la création de formes complexes et de tolérances extrêmement strictes. Le processus de conception prend également en compte les rayons de jeu, de cisaillement et de pliage pour garantir un emboutissage efficace et cohérent sans endommager la plaquette ou la pièce.
Processus de fabrication et contrôle qualité
La production d'inserts de poinçonnage de précision nécessite des capacités de fabrication avancées. Des techniques telles que l'électroérosion, la découpe au laser et le meulage sont couramment utilisées pour obtenir la précision dimensionnelle et la finition de surface requises. L'électroérosion, en particulier, excelle dans la production de formes complexes et de détails fins, souvent utilisés pour créer des caractéristiques complexes dans la géométrie de l'insert. Les processus de meulage sont essentiels pour obtenir la finition de surface nécessaire, qui a un impact direct sur la qualité des pièces embouties et la longévité de l'insert lui-même.
Des mesures rigoureuses de contrôle de la qualité sont essentielles tout au long du processus de fabrication. Des contrôles dimensionnels à l'aide de machines de mesure tridimensionnelle (MMT) garantissent que la plaquette est exactement conforme aux spécifications de conception. Des mesures de rugosité de surface sont également effectuées pour vérifier la qualité de la finition de surface. Ces étapes de contrôle de la qualité sont essentielles pour garantir la production constante de plaquettes de haute qualité, réduire les temps d'arrêt et améliorer l'efficacité globale de l'opération d'emboutissage.
Applications dans divers secteurs industriels
Les applications des inserts de poinçonnage de précision couvrent un large éventail d'industries. Dans le secteur automobile, ils sont utilisés pour créer des pièces complexes pour les véhicules, des panneaux de carrosserie et des composants de châssis aux mécanismes internes complexes. L'industrie électronique utilise ces inserts pour produire des connecteurs, des bornes et divers autres composants petits mais essentiels. D'autres secteurs tels que la fabrication d'appareils électroménagers, l'aérospatiale et la production de dispositifs médicaux dépendent également fortement de l'emboutissage des métaux, les inserts de poinçonnage de précision jouant un rôle clé dans leurs processus de fabrication
La polyvalence de ces inserts permet de créer une vaste gamme de formes et de tailles, les rendant ainsi adaptables aux besoins spécifiques de chaque industrie. Des formes simples aux géométries très complexes, ces inserts garantissent que l'emboutissage des métaux reste une méthode rentable et efficace pour produire des pièces de grande précision en grande quantité.