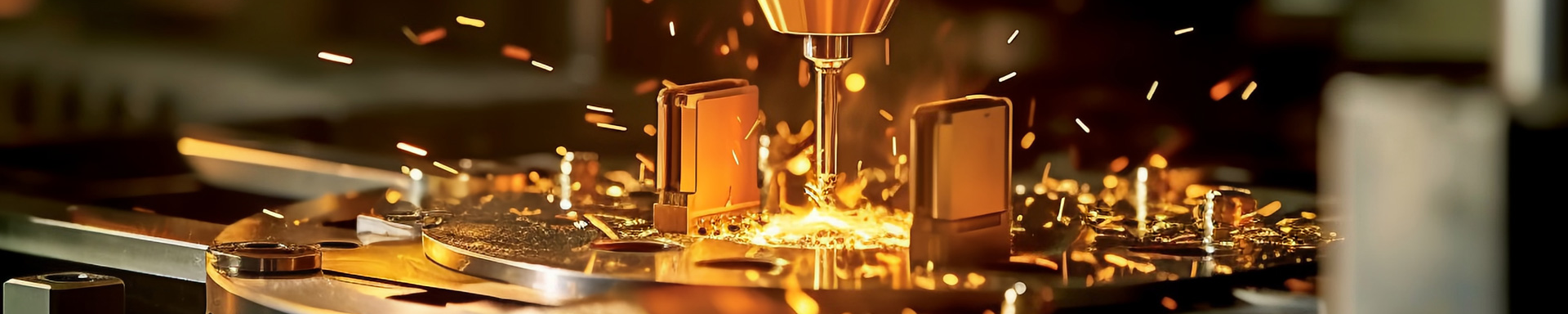
Techniques avancées dans les procédés de moulage sous pression pour automobiles
2024-11-22 15:41Améliorations apportées au moulage sous pression à haute pression (HPDC)
Le moulage sous pression haute pression (HPDC) reste une pierre angulaire de la production de composants automobiles, apprécié pour sa rapidité et sa capacité à créer des pièces complexes. Cependant, le moulage sous pression haute pression traditionnel a souvent du mal à obtenir une précision dimensionnelle et une qualité de surface constantes sur de grands lots. Les améliorations modernes se concentrent sur l'optimisation de l'ensemble du processus, de la conception de l'outil et de la sélection des matériaux aux paramètres d'injection et aux techniques de post-traitement. Cela comprend des avancées dans les matériaux de l'outil qui offrent une résistance à l'usure et des propriétés de transfert de chaleur supérieures, ce qui conduit à une durée de vie prolongée de l'outil et à une meilleure qualité des pièces. En outre, la mise en œuvre de systèmes de contrôle sophistiqués permet une surveillance et un réglage précis des paramètres tels que la pression d'injection, la vitesse et le temps de maintien, minimisant ainsi les variations et garantissant des résultats cohérents.
Un autre domaine d’amélioration essentiel est l’utilisation de logiciels de simulation. Ces programmes avancés permettent aux ingénieurs de tester virtuellement différentes conceptions de matrices et paramètres d’injection avant le début de la production réelle. Cette capacité prédictive réduit considérablement le besoin de prototypage physique et d’itérations coûteux, accélérant ainsi le processus de développement et minimisant les déchets. L’intégration de capteurs sophistiqués dans la machine de moulage sous pression fournit un retour d’information en temps réel, améliorant encore le contrôle du processus et optimisant le résultat. Cette approche basée sur les données conduit à des améliorations significatives de la qualité des pièces, réduisant les défauts et augmentant l’efficacité globale.
Coulée sous pression à parois minces
La demande de véhicules légers pousse à la coulée sous pression à parois minces. Cette technique permet de créer des composants avec des épaisseurs de paroi considérablement réduites tout en préservant l'intégrité structurelle. Cela contribue non seulement à la réduction du poids, mais aussi à la réduction des coûts de matériaux. Cependant, la réalisation d'une coulée à parois minces nécessite un contrôle précis du processus d'injection et l'utilisation de matrices spécialisées. Les techniques avancées utilisent des conceptions de matrice optimisées avec des systèmes de refroidissement améliorés pour assurer une solidification rapide et éviter les défauts tels que la porosité ou le gauchissement. Le développement d'alliages d'aluminium à haute résistance spécifiquement adaptés aux applications à parois minces améliore encore la faisabilité et la résistance de ces composants.
Le procédé bénéficie également d'innovations dans la conception des matrices, intégrant des fonctionnalités telles que des systèmes de distribution optimisés et des stratégies de ventilation pour améliorer le flux de métal et minimiser l'emprisonnement d'air. Les simulations avancées jouent un rôle crucial dans la prévision des problèmes potentiels et l'optimisation des paramètres du procédé pour obtenir la géométrie de paroi mince souhaitée tout en maintenant l'intégrité structurelle et la qualité de surface. La mise en œuvre de systèmes de surveillance et de contrôle en temps réel minimise encore davantage les défauts et garantit une production constante de composants de haute qualité.
Coulée sous pression multi-matériaux
L'intégration de plusieurs matériaux dans un seul composant moulé sous pression ouvre des possibilités intéressantes pour améliorer la fonctionnalité et les performances. Cette approche permet de combiner des matériaux aux propriétés différentes, telles que la résistance, la conductivité thermique et la conductivité électrique, au sein d'une même pièce. Par exemple, un composant peut incorporer un noyau en alliage d'aluminium à haute résistance pour l'intégrité structurelle, combiné à un matériau plus souple et plus ductile dans des zones spécifiques pour améliorer la fonctionnalité ou réduire l'usure. Cela nécessite une conception de matrice sophistiquée et un contrôle précis du processus d'injection pour garantir un placement et une liaison précis des différents matériaux.
Les techniques avancées de moulage sous pression multi-matériaux impliquent souvent l'utilisation d'inserts spécialisés dans le moule pour définir les limites des différents matériaux. Un contrôle précis des paramètres d'injection est essentiel pour éviter le mélange ou le délaminage des différents matériaux. L'utilisation de logiciels de simulation est particulièrement essentielle pour optimiser les paramètres de conception et de processus, garantissant ainsi l'intégration et le collage réussis de plusieurs matériaux dans le composant final. Le développement de nouvelles techniques d'assemblage, telles que le soudage par friction-malaxage ou le soudage par diffusion, joue également un rôle important dans la création de pièces moulées multi-matériaux robustes et fiables.
Matériaux et revêtements de matrices avancés
Les performances et la longévité des matrices de moulage sous pression ont un impact significatif sur l'efficacité globale et la qualité du processus. Les matériaux de matrice traditionnels, bien que fonctionnels, présentent souvent des limites en termes de résistance à l'usure, de conductivité thermique et de résistance à la corrosion. Les avancées modernes se concentrent sur le développement et l'application de matériaux de matrice innovants, tels que les alliages d'acier avancés, les composites céramiques et les nouveaux revêtements. Ces matériaux offrent une durabilité accrue, permettant des taux de production plus élevés et une durée de vie prolongée des matrices.
Des revêtements spéciaux, appliqués sur la surface de la matrice, améliorent encore la résistance à l'usure, réduisent la friction et améliorent la finition de surface des composants moulés. Ces revêtements peuvent être adaptés à des applications spécifiques, offrant des propriétés personnalisées telles qu'un meilleur transfert de chaleur ou des caractéristiques de démoulage. Le développement de revêtements plus durables et plus fiables est en cours, l'accent étant mis sur l'obtention d'une résistance à l'usure encore plus élevée et l'amélioration de la qualité globale des pièces moulées. Cela permet d'augmenter les taux de production et d'améliorer la qualité des composants, tout en minimisant les temps d'arrêt associés à la maintenance et au remplacement de la matrice.